How to Reduce Downtime and Save on H₂S Removal Costs
H₂S (Hydrogen Sulfide) is a hazardous chemical compound that can be produced from human, agricultural, and industrial activities. It’s present in every biogas project. Due to its impact on health, safety, the environment, and downstream equipment, it must be removed before biomethane or renewable natural gas (RNG) is ready for pipeline use. Greenlane’s Cascade H2S removal solution is proven and effective for applications with a high concentration of H₂S and/or high flow rate.
Common H₂S Removal Problems
H₂S management poses significant challenges for biogas facility owners and developers, such as municipal waste facilities, dairy farms, and water treatment plants. Even in ambient conditions, it is extremely hazardous for operators. It can also corrode equipment, increasing downtime for repairs and causing costly safety risks.
One of the most common problems biogas facilities face when it comes to removing H₂S is the reliability of the equipment in various process conditions. Unsuitable equipment can lead to safety hazards, downtime, and ultimately higher operational costs, especially for plants facing a high mass flow rate of H₂S.
Many biogas projects utilize passive media for H₂S removal. The media becomes saturated by the H₂S and will eventually need to be replaced. Choosing the correct media and bed size is critical to an efficient removal of H₂S. Parameters like the H₂S concentration, relative humidity, loading rate, and temperature will need to be properly accounted for. Sometimes in the development of biogas projects, the H₂S can be significantly underestimated when normal operation begins. When this happens, media can quickly become saturated and require frequent replacement. To maintain proper H₂S removal, the system must be partially or sometimes entirely taken offline to swap out the spent media, leading to downtime and lost profit. While utilizing bigger media tanks may seem like a solution, it can prove to be expensive and impractical if the plant is already operational.
Scrubbing systems offer another approach to H₂S removal. Chemical scrubbing systems can be complex, difficult to operate, and dirty, while biological scrubbing systems can be extremely sensitive to changes in factors such as biogas composition, flow rate or the H₂S concentration. In these biological systems, a healthy culture is key to the effectiveness of the technology. If these factors fluctuate outside the normal operating range, the bacteria may not be able to effectively remove the H₂S, or may completely die off, requiring downtime or a complete system restart.
Misconceptions About H₂S Removal
An underestimated aspect of H₂S removal is the proper preconditioning of the biogas. Production equipment is naturally a cost center of a biogas system, which often results in less education in and understanding of the preconditioning segment of the process.. In reality, proper preconditioning is essential for reliable and effective grid-ready RNG production. Neglecting it can lead to significant operational problems down the line.
Proper preconditioning solutions are influenced by factors like flow rate, H₂S concentration, and the presence of other contaminants. The right choice in H₂S removal technology is the one that addresses those factors with a balance of reliability, effectiveness, and cost-efficiency.
The High Cost of Neglecting H₂S Removal
Failing to effectively remove H₂S can destroy a facility’s profitability. Malfunctioning systems lead to prolonged downtime and high operating costs. For example, a plant with a failed biological scrubber was forced to rely on a smaller passive media unit. It required daily media replacement, limiting operation significantly and requiring unmanageable media costs.
Additionally, Improper removal of H₂S can introduce safety risks to both humans and downstream equipment, adding to the “high cost” of neglecting this part of the biogas process.
In North America, many operators believe passive media is the most cost-effective H₂S removal solution. However, the solution is inherently non-regenerative and will require media replacements over time. This may translate to high operational costs in the form of the purchase and disposal of carbon-based media, revenue lost to downtime, and maintenance labor. In most European regions, biogas facilities have historically addressed the issue by employing a two-step process for H₂S treatment. First, injecting air or oxygen into digesters, and second, treating the biogas with passive media systems. However, this approach isn’t viable in North America due to stringent pipeline regulations for oxygen.
Greenlane’s Cascade H2S system offers a more economical and effective approach. Cascade H2S is a bulk H₂S reduction system and when paired with a small polisher will meet any strict pipeline requirement. Additionally, the unique design philosophy of treating biogas at a low pressure with an intended outlet of <100 ppm of H₂S, allows for a competitive investment cost and a reduced total cost of ownership.
In some situations, Greenlane’s Cascade H2S paired with a small passive media polisher can offer near-immediate cost savings. Instead of aiming to completely remove H₂S down to pipeline specifications, Cascade H2S focuses on achieving a bulk reduction of H₂S. Biogas is fed into the bottom of a scrubbing tower where it is treated with a chemical solution. The treated gas exits through the top of the scrubber, typically with over 90% of the H₂S removed. When required, a small passive media system then completes the process by polishing this biogas to meet consumer specification.
The diagram below outlines the basic process of the Cascade H2S.
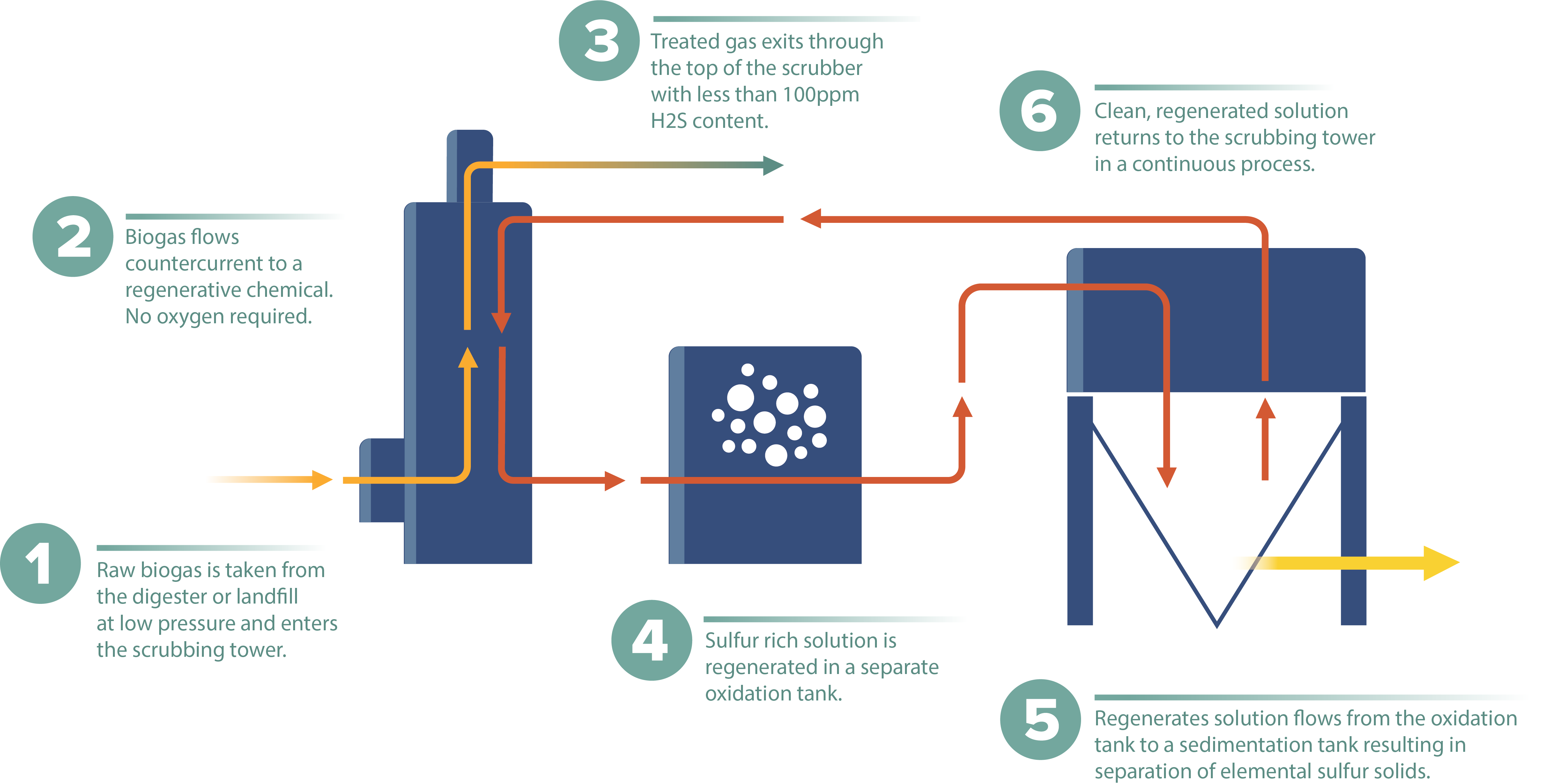
This graph illustrates the cost savings potential of a Cascade H2S system compared to a passive media-only system. Facilities operating on the high side of the curve would quickly see significant cost savings.
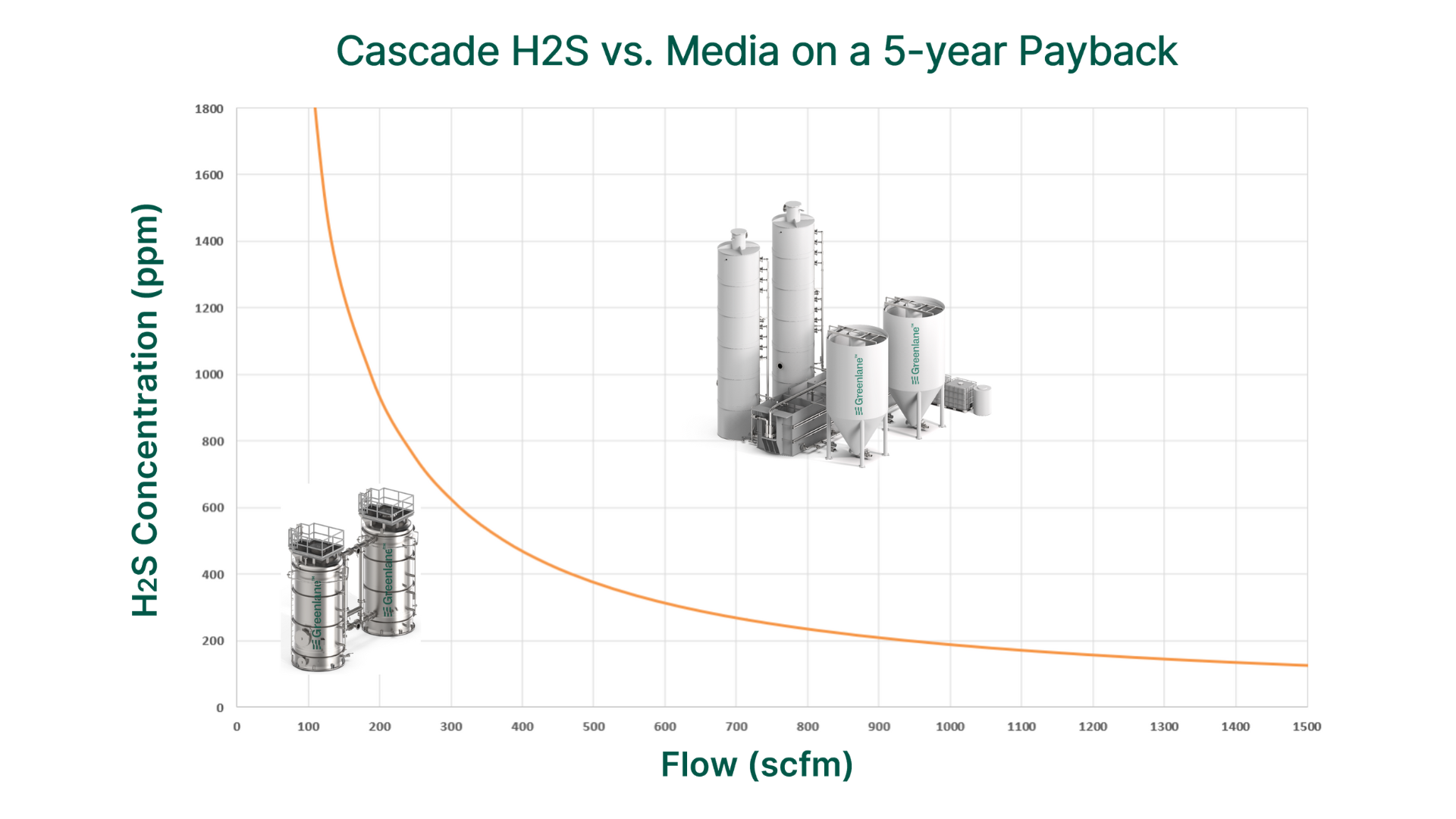
The Cascade H2S system offers numerous advantages over other H₂S removal systems. Unlike some systems that require complex setups and biological processes to mature before functioning, Cascade H2S boasts a faster path to operation. Its prefabricated and pretested design allows for a quick plug-and-play installation.
The Cascade H2S system operates at the same low pressure as the incoming biogas, eliminating the need for additional pressurization steps. This translates to lower energy consumption and potentially reduced equipment costs. An added benefit is the generation of a sulfur-rich byproduct suitable for use as a fertilizer, potentially creating an additional revenue stream for the facility.
While this technology is newer to the North American market, biogas facility owners and developers can be confident, given Greenlane’s proven track record. There are over 160 Cascade H2S systems installed worldwide, including several commissioned in North America. The Greenlane Cascade H2S system is the right choice for facilities seeking a reliable and cost-effective H₂S Solution.
For more information about the Greenlane Cascade H2S removal solution, as well as other solutions, click here.